WHAT IS STAMPING?
The metal stamping process is used to manufacture parts and components from flat metal sheets or coils. The process involves the application of pressure (and if necessary heat) to transform the metal into parts of different shapes and sizes. The parts can be flat and simple in profile, or they can be more complex and have more detailed shapes.
For this process, presses of different sizes (tonnage) and shapes are used to exert pressure on the metal. This is a very accurate process that allows parts to be produced with high levels of detail and tolerance. It is a widely used technique in the automotive industry and is used to manufacture a wide variety of parts and components, such as the body, chassis and battery casing of hybrid and electric vehicles.
In their most basic operation, presses work with a die and a punching tool. A die is a tool that has the desired shape of the workpiece, while a punch tool is used to cut the metal following the contour of the die.
Additional forming steps are often used to produce complex parts and profiles. Such additional operations may include stretching, flanging and laminating, among others. These additional stages allow the production of parts with more complex and detailed shapes and profiles.
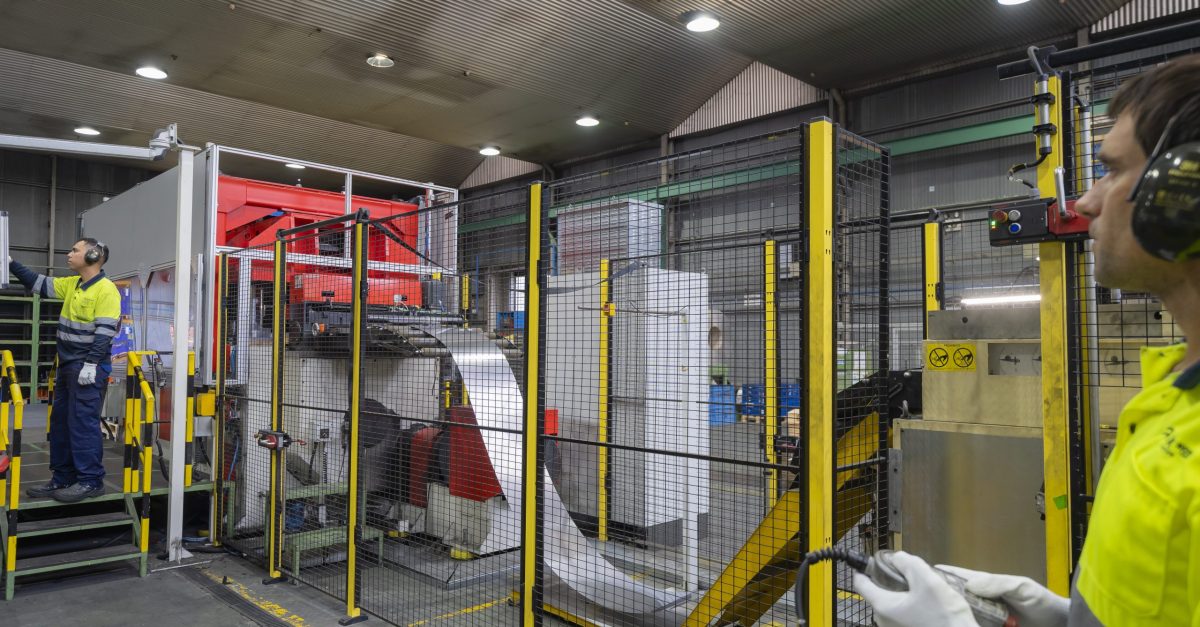
THE STAMPING PROCESS
The process is explained in detail from start to finish:
Die design: The first step is the design of the die, the tool that will be used to shape the material. This design is created using computer-aided design (CAD) software.
Die manufacturing: Once the design has been made, the stamping die is manufactured using a CNC (Computer Numerical Control) machine or by the laser cutting process.
Preparation of the material: If a simple die is used, metal sheets are cut to the required length. For a progressive die, a coil will be used for continuous feeding into the die.
Machine adjustment: Machine parameters such as the stamping force (press tonnage) and the operating speed are adjusted to ensure that the process is carried out correctly.
Stamping process: Once the material has been prepared and placed in the machine, the stamping process begins. The press exerts the necessary pressure to deform the material into the desired shape using the die.
Heat treatment: In some cases, heat treatment may be applied to the stamped material to improve its mechanical properties and strength.
Cleaning and finishing: Once the stamping process has been completed, the stamped parts are cleaned and finished.
WHAT IS A DIE?
After learning about the stamping process, we will analyse the die, one of its main tools. This tool comprises a punch and a die; the punch has the shape and dimension of the desired final shape, and the die is a hardened block of steel with a cavity that is the inverse of the shape of the punch.
For stamping, the metal part is placed between the punch and the die. The punch and die are then pressed together either mechanically or hydraulically. The punch embosses the metal part into the desired shape, and the excess material is removed from the die.
Die cutting is therefore a type of stamping in which a die is used to cut and shape a material. This technology is widely used in the automotive industry to manufacture metal parts and components for vehicles.
WHAT ARE THE TYPES OF DIE-CUTTING?
Depending on how complex the process is and the number of operations required in the manufacturing process, we can speak of three types of die-cutting:
Simple die: this is the most basic type of die and is used to cut and shape metal parts by using a single cutting tool. It is the best option for simple parts with simple shapes and little or no forming operations.
Composite die: This die uses multiple cutting and forming tools to produce parts with more complex shapes, and is suitable for parts that require multiple cutting and forming operations to shape.
Progressive die: This process uses a sequence of workstations to produce parts with very complex shapes. Each station of the progressive die performs a different cutting or forming operation, and the part is fed through the die as each operation is completed. The progressive die is suitable for producing high volume parts with high precision and repeatability.
DIFFERENT DIE TYPES
The above classification is based on the complexity of the parts and also defines the process itself. But we can also classify the dies according to the desired features of the part.
Thus, some of the most common die types are:
Cutting die: used to cut metal parts into specific shapes.
Bending die: used to bend metal parts at specific angles.
Deep-drawing die: used to shape a metal part by making it penetrate into an enclosed space.
Drilling die: used to make holes in parts.
Punching die: a specialised tool used to cut or shape materials, usually sheet metal or plastic, by applying pressure with a punch.
Forming die: tool used to shape metal parts, e.g. to make a flat part into a curved shape or to make a part have a special cross-section.
Forging die: used to shape metal parts through the use of high temperatures and pressure.
Stamping die: the stamping die is a tool used to shape metal parts through the use of high temperatures and pressure.

ADVANTAGES OF DIE-CUTTING
Die-cutting is an Industrial manufacturing process that has a number of important advantages, which explains its widespread use. One of the main advantages of die-cutting is precision. This technology makes it possible to manufacture high quality parts to very tight tolerances, which is especially important when it comes to parts that must fit or work together precisely.
Another advantage of die-cutting is its versatile nature, as it allows parts of different shapes and sizes to be produced. In addition, different types of dies can be used to shape sheet metal in different ways, which means that die cutting is suitable for a wide variety of applications.
In addition, it is a technology that allows mass production. This enables fast and efficient manufacturing, which is beneficial for companies looking to increase their production capacity. In addition, die-cutting can be more economical than other processes.
Parts produced by the die-cutting process are generally stronger and more durable than those produced by other processes. This is due to how the metal is shaped through the use of a die. In addition, the die-cutting process is relatively efficient in terms of energy consumption. This makes it an appealing option for companies looking to reduce their carbon footprint.
AUTOMOTIVE APPLICATIONS OF DIE-CUTTING
Among the types of automotive parts that can be manufactured using this technology, we would highlight the following:
Body: metal parts forming the body of a vehicle.
Suspension components: steel or aluminium components that form part of the suspension of a vehicle such as swing arms.
Engine components: metal parts that are part of a vehicle engine, such as pistons, connecting rods and crankshafts.
Battery components: battery housing and/or covers.
Die-cutting is a process widely used in the automotive industry as it allows the production of precise, high quality parts on a large scale, which is essential for the manufacture of high quality vehicles.